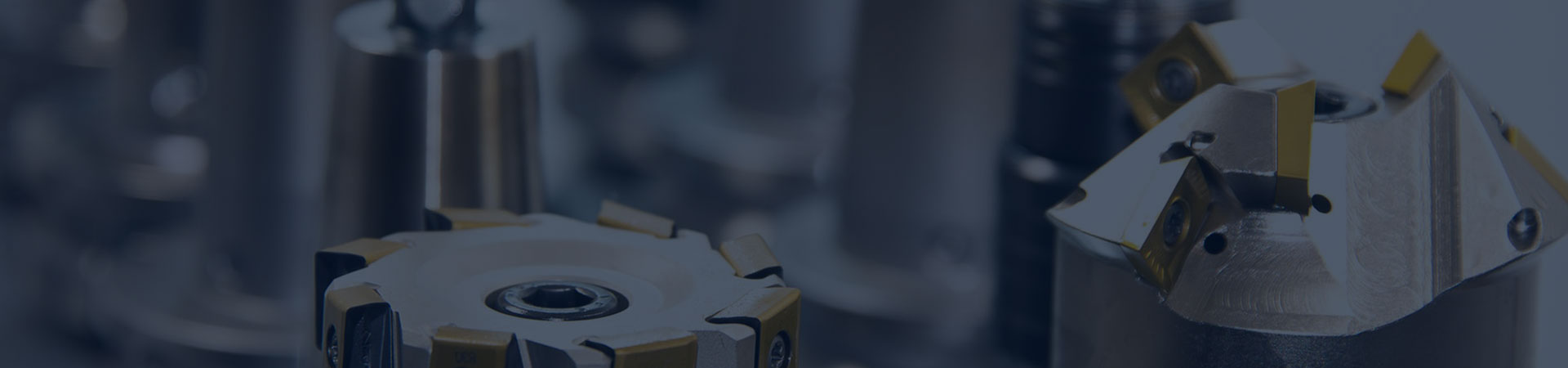
What is polymer bearings
Marine polymer bearings are bearings designed specifically for marine applications and are made of polymer materials. Compared with traditional metal bearings, polymer bearings have many unique advantages, making them excellent in marine environments.
Self lubrication: Many polymer materials have self-lubricating properties, which do not require additional lubricating oil, reducing maintenance workload and operating costs.
Corrosion resistance
Low friction coefficient
Wear resistance
Shock absorption
Overview
Marine polymer bearings have become indispensable components in modern shipbuilding and marine engineering due to their unique material properties and various advantages. Its characteristics of corrosion resistance, low friction, self-lubricating, and wear resistance make it outstanding in various marine environments, providing reliable and efficient operational support.
For more marine rudder system components, kindly please click here.
Terms and definitions
1. Gauge length L0: the initial distance between the two mark lines in the middle portion of the test specimen, expressed in millimeter (mm);
2. Test velocity v: the velocity at which the two pressing plates of the testing machine approach each other or the grippers depart from each other during the test, expressed in millimeter per minute (mm/min);
3. Compressive stress σ: the compressive load borne by the original cross-sectional area of each unit of the test specimen, expressed in megapascal (MPa);
4. Compressive strength σM: the maximum stress borne by the test specimen during the test, expressed in megapascal (MPa);
5. Compressive strain ε: the reduction in length of each unit of original gauge length, expressed by ratio or percentage (%);
6. Tensile stress σ: the tensile load applied on each unit of original cross-sectional area within the gauge length of the test specimen at any given time, expressed in megapascal (MPa);
7. Tensile break stress σB: the tensile stress at which the test specimen breaks, expressed in megapascal (MPa);
8. Tensile strength σM: the maximum tensile stress borne by the test specimen during the tensile test, expressed in megapascal (MPa);
9. Linear expansion coefficient: the ratio of length variation of the test specimen to its original length at each temperature change of 1 degree centigrade, expressed in °C-1.
Materials and components
Caprolactam particles.
Additives such as molybdenum disulfide, graphite, carbon black, etc.
Reinforcing fibers such as glass fiber.
Technical requirements
1. Compressive strength
The direction of test for strip-shaped bearings is to be parallel to the extrusion face and the compressive strength is to be more than or equal to 85MPa;
If the direction of test is to be vertical to the extrusion face, the compressive strength is to be more than or equal to 120MPa;
2. Tensile strength
The tensile strength is to be more than or equal to 70MPa.5.3 Temperature resistance
The test results are not to be less than 80% of the results obtained from tests at normal temperature.
3. Seawater resistance
The test results are not to be less than 80% of the results obtained from tests at normal temperature.
4. Volume expansion in lubrication medium
The measured volume expansion ratio of test specimens is not to be greater than 3%.
5. Friction factor
Friction factor is not greater than 0.25.
Characteristic
Corrosion resistance: Polymer materials have excellent corrosion resistance, which can effectively resist the erosion of seawater and other chemicals, and extend the service life of bearings.
Low friction coefficient: Polymer bearings have a lower friction coefficient, which can reduce friction losses and improve operating efficiency.
Self lubrication: Many polymer materials have self-lubricating properties, which do not require additional lubricating oil, reducing maintenance workload and operating costs.
Wear resistance: Polymer materials have good wear resistance and can be used for a long time under high loads and high-speed conditions without being easily worn.
Shock absorption: Polymer materials have good shock absorption performance, which can effectively absorb and alleviate vibration and impact during operation, protect equipment, and extend service life.
Typical applications
Marine polymer bearings are widely used in the following ship systems:
Rudder system: used to support and guide the rudder shaft, ensuring flexible rotation of the rudder.
Propulsion system: including propeller bearings and shaft support, reducing friction and improving propulsion efficiency.
Deck machinery: bearings for equipment such as windlass and winch, providing reliable support and operational support.
Other marine equipment, such as underwater detection equipment and marine platform equipment, require corrosion-resistant and wear-resistant bearings.
Advantages
Long service life: The corrosion and wear resistance characteristics of polymer bearings make their service life long, reducing replacement frequency and maintenance costs.
Environmental protection: Due to the absence of lubricating oil, polymer bearings reduce environmental pollution and meet modern environmental requirements.
Lightweight: Polymer materials are lighter than metals, helping to reduce the overall weight of ships and improve fuel efficiency.
Low maintenance: The self-lubricating and corrosion-resistant characteristics greatly reduce the maintenance workload of polymer bearings, improving the reliability and availability of equipment.