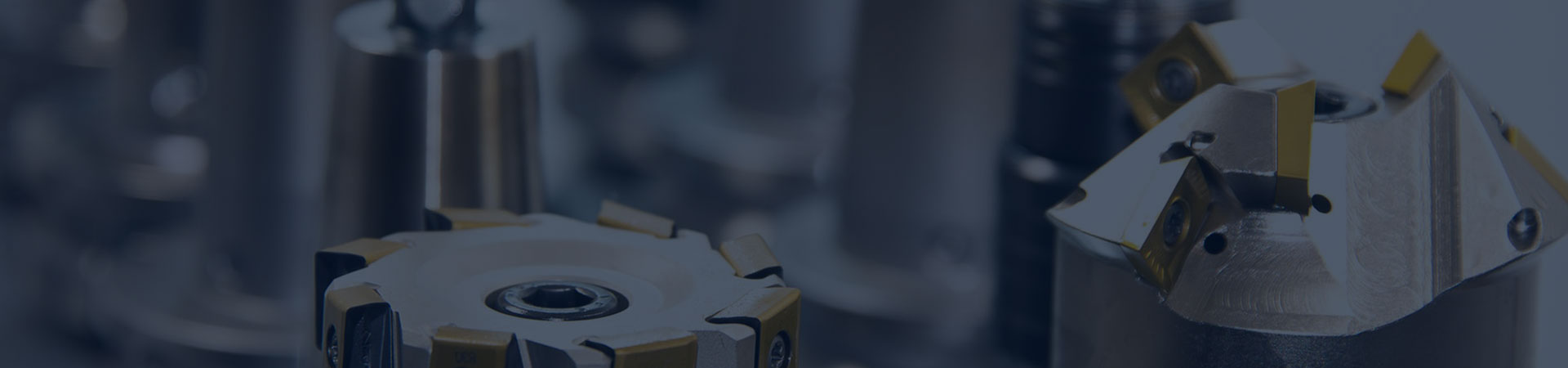
What are the cooling methods for marine air compressors
There are two main cooling methods for marine air compressors: air cooling and water cooling.
Overview
1. Air -Cooled
During the compression process, as the pressure increases, the temperature of the air also increases. In order to reduce power consumption and exhaust specific volume, increase cylinder storage, and increase exhaust volume, cooling is required for both low-pressure and high-pressure exhaust stages, known as inter stage cooling and post cooling, respectively.
Interstage cooling refers to the cooling of the low-pressure exhaust gas. Interstage cooling has a significant effect on reducing exhaust temperature and power consumption, and generally requires cooling water to pass through the interstage cooler first. Interstage coolers often use shell and tube type, where cooling water flows through several baffles inside the shell in a zigzag manner from bottom to top, while compressed air flows through the pipes from top to bottom.
Post cooling refers to the cooling of the high-pressure exhaust. Post cooling can reduce the specific volume of exhaust gas, increase the storage capacity of gas cylinders, alleviate the degree of pressure drop, and make the vapor of oil and water in the exhaust condense and facilitate separation. Generally, cooling to around 60 ℃ is sufficient. Some ships, in order to reduce equipment, do not install air compressors for post cooling. In this case, it is even more important to promptly release the oil and water from the storage cylinders.
(1) Working principle:
The air-cooled air compressor takes away the heat generated during the compression process through the flow of air.
The cylinder and other high-temperature components of the compressor are equipped with heat dissipation fins to increase the heat dissipation area.
Air cooling systems are usually equipped with fans, which accelerate air flow and improve heat dissipation through forced convection.
(2) Advantages:
Simple structure and easy maintenance.
No external cooling water source is required, suitable for environments with limited space such as ships.
Suitable for small and medium-sized air compressors, with lower cost.
(3) Disadvantages:
The heat dissipation effect is greatly affected by environmental temperature and fan performance.
For large high-power air compressors, the heat dissipation effect may not be ideal.
2. Water-Cooled
Marine air compressors are commonly cooled with seawater, and to reduce corrosion, anti-corrosion zinc rods should be installed in the cooler. To prevent excessive pressure in the cooling water chamber due to exhaust leakage, a safety film 12 is also installed. The cooling water process of a typical marine air compressor is as follows: the cooling water first enters the air cooler, undergoes inter stage cooling and then post cooling. The cooling water from the post cooler is further divided into two paths, one of which flows from bottom to top through the cooling water chambers of the cylinder and cylinder head. If the high and low pressure cylinders are arranged separately, they are usually connected in series, with low first and then high; The other way enters the oil cooler located inside the crankcase. There is a water inspection cock on the inlet pipe of the cooling water. The lower part of the cylinder is equipped with a drain plug 21 to empty the cooling water chamber before repairing the air compressor, and can also be used to check whether the cooling water pressure meets the requirements.
(1) Working principle:
The water-cooled air compressor takes away the heat generated during the compression process through the circulation of cooling water.
The cylinder and other high-temperature components of the compressor are equipped with cooling water channels, through which cooling water flows and absorbs heat.
After absorbing heat, the cooling water is pumped to a heat exchanger or cooling tower, cooled through heat exchange with external air or seawater, and then recycled for use.
(2) Advantages:
Good heat dissipation effect, suitable for large high-power air compressors.
The heat dissipation effect is stable and not easily affected by environmental temperature.
Can maintain good cooling performance in high temperature and high load working environments.
(3) Disadvantages:
The structure is relatively complex, with high initial investment and maintenance costs.
A stable cooling water source is required, suitable for ships with seawater or freshwater cooling systems.
The cooling system may require additional equipment such as water pumps, heat exchangers, etc.
3. Factors to consider when choosing a cooling method
Compressor power and scale: Small and medium-sized air compressors usually choose air-cooled, while large high-power air compressors often choose water-cooled.
Environmental conditions: In environments with limited space such as ships, air-cooled systems are often preferred due to their simple structure. In environments with sufficient cooling water resources, water cooling systems are more suitable due to their efficient heat dissipation performance.
Cost and maintenance: Air cooling systems have lower costs and are easy to maintain, but their heat dissipation effect is relatively poor; The water cooling system has good heat dissipation effect, but its structure is complex, the cost is high, and maintenance is also cumbersome.
The choice of cooling method for marine air compressors depends on specific application requirements, equipment scale, and environmental conditions. Air cooling and water cooling each have their own advantages and disadvantages, which need to be comprehensively considered according to the actual situation.
For more marine air compressor information, please click here.