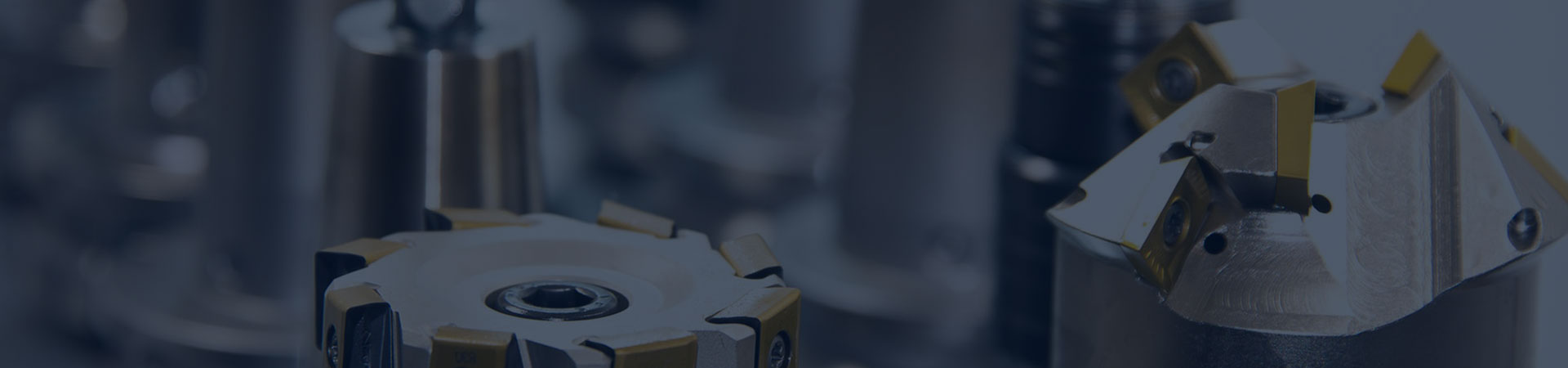
The Difference Between Fibre And Steel Wire Rope Cores
Core is central element of a round rope around which are laid helically the strands of a stranded rope or the unit ropes of a cable laid rope. The function of the rope core is mainly to support and reduce the pressure between the strands, and the fiber rope core also plays the role of lubrication, anti-corrosion and oil storage.
Overview
Core types
Fiber wire rope cores(FC)
Fiber core made from either natural fibers(NFC) or synthetic fibers(SFC).
A.Natural fibers(NFC):such as sisal, synthetic fiber, cotton yarn, jute, etc. or other fibers that meet the requirements.
B.Synthetic fibers(SFC):Polyethylene, polypropylene, asbestos, etc.
Fiber cores are normally prodyced inthe sequence fibers to yarns, yarns to strands to rope.
Advantages:
Greater flexibility, good bending performance, good toughness.
Acid resistance, alkali resistance.
Lightweight and easier to handle and transport.
Store lubricating oil to extend the life of the rope.
High strength to weight ratio.
Disadvantages:
Lower crush resistance
Cannot be used in high-heat environments
Lower strength than steel in some applications
Application:
Elevator wire rope
Fishing wire rope
Mooring wire rope
Towing and luffing ropes
Wire rope for various lifts, winches in seawater operations.
Steel wire rope core(WC)
Core made from steel wires arranged as a wire strand(WSC) or as an independent wire rope(IWRC). The steel core/or its outer strands can also be coverd with either fiber or solid polymer. The stranded rope core is normally made as a separate unit, the exception being where the core is closed in parallel with the outer strands, designated PWRC.
Advantages:
Higher strength
high crush resistance
High temperature resistance
Widly applications
Disadvantages:
Lower flexibility than fiber core wire rope.
Poor resistance to bending deformation than fiber core wire rope.
Application:
Suitable for most applications.