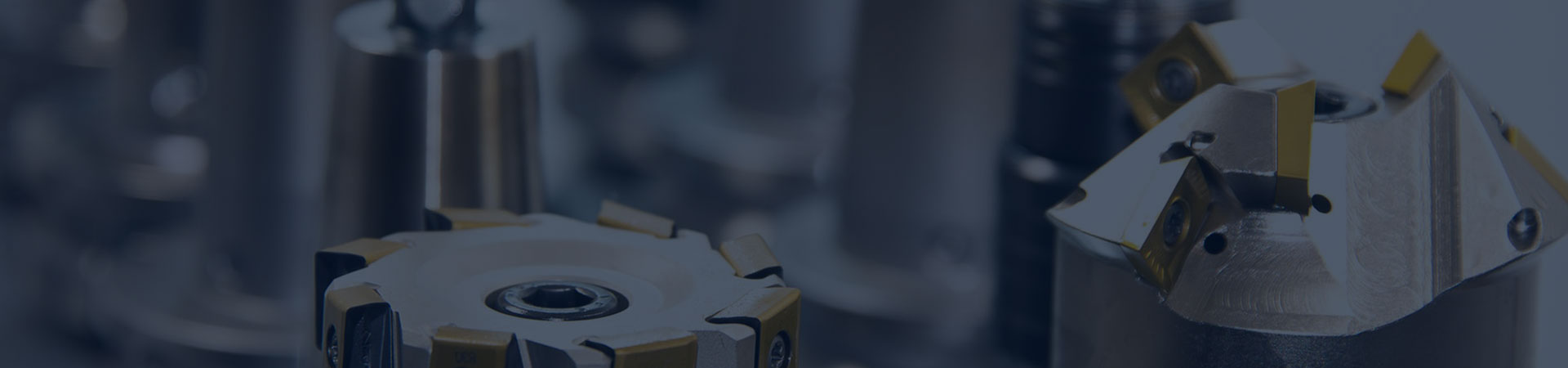
Common materials and craft types for marine passenger chairs
Marine passenger chairs commonly use fabric, natural leather, and high-quality synthetic leather. Fabric offers good breathability and stability but is less resistant to dirt. Natural leather, though comfortable and moisture-absorbent, can be slippery and costly to maintain. High-quality synthetic leather, made of PU or PVC, is durable, abrasion-resistant, and available in various colors, suitable for both indoor and outdoor chairs. Each material type offers distinct advantages and considerations for marine seating.
Overview
Fabric
Fabric has good covering and breathability. It provides a greater friction force when users sit on it, offering a more stable and comfortable feeling. Fabric comes in a wider range of colors and patterns compared to leather, with a high cost-performance ratio, but it is less resistant to dirt and harder to clean.
Natural Leather
Natural animal leather, also known as genuine leather, is mainly composed of collagen. It has a certain elasticity, breathability, and moisture absorption and wicking properties. Even when completely dried in its natural state, leather still contains 15% moisture. When suede leather reaches 70% of its weight in water absorption during processing without harmful chemicals, it can be in close contact with the human body, providing strong comfort and ease of cleaning. However, genuine leather may feel too slippery and is prone to surface damage, leading to higher maintenance costs.
High-Quality Synthetic Leather
High-quality synthetic leather is adopted PU or PVC coating. PU coating is not waterproof or sun-proof, it is suitable for indoor chairs, instead PVC coating can be used in outdoor chairs. Compared to natural leather, high-quality synthetic leather has a higher utilization rate, stronger abrasion resistance, is easy to cut, and offers a variety of colors and patterns to choose from.
The differences between PVC and PU
1. Manufacturing Process
PVC Leather: Plastic granules are first melted and stirred into a paste, which is then evenly coated on a T/C knitted fabric base to the specified thickness. It then enters a foaming furnace to foam, making it adaptable to various products with different softness requirements. Surface treatment such as dyeing, embossing, polishing, matting, and fuzzing is carried out simultaneously upon exiting the furnace, according to specific product requirements.
PU Leather: PU leather manufacturing is more complex than PVC leather because PU uses canvas PU material with good tensile strength as the base fabric. Besides being coated on top of the base fabric, PU can also encapsulate the base fabric in the middle, making the base fabric invisible. PU leather has better physical properties than PVC leather, including better flexibility, tensile strength, and breathability (which PVC lacks).
2. Different way to put the pattern and color
PVC leather patterns are created through hot-pressing with steel pattern rolls. PU leather patterns are made by first heat-pressing a pattern paper onto the semi-finished leather surface, allowing it to cool before separating the paper leather and proceeding with surface treatment.
3. Price and Cost
PU leather is priced at least double that of PVC leather, and for certain special requirements, PU leather can be two to three times more expensive than PVC leather. The pattern paper used for PU leather can typically only be used 4-5 times before being discarded, while pattern rolls have a longer usage cycle, contributing to higher production costs for PU leather compared to PVC leather.
4. Identification Methods for PVC and PU
PU feels softer, has better quality and resilience, and is generally used for fabrics that can withstand greater tensile forces.PVC is denser than PU.
PVC's patterns are deeper, and the foaming layer is more visible in the middle compared to PU.
PVC material is thick stiff, but not sturdy. the PU surface is sturdy, but easily scratched or destroyed.
Basically both material can be lead/naphthalene free and safe, but it may need to put more additives in the process of making PVC, especially the process for making PVC softer. In a word if we tailor made them, both can be safe, but if we use market available material, PU material is much more safer than PVC one.
Temperature resistance for PVC is 65 degree Celsius , and PU can up to 95 degree Celsius