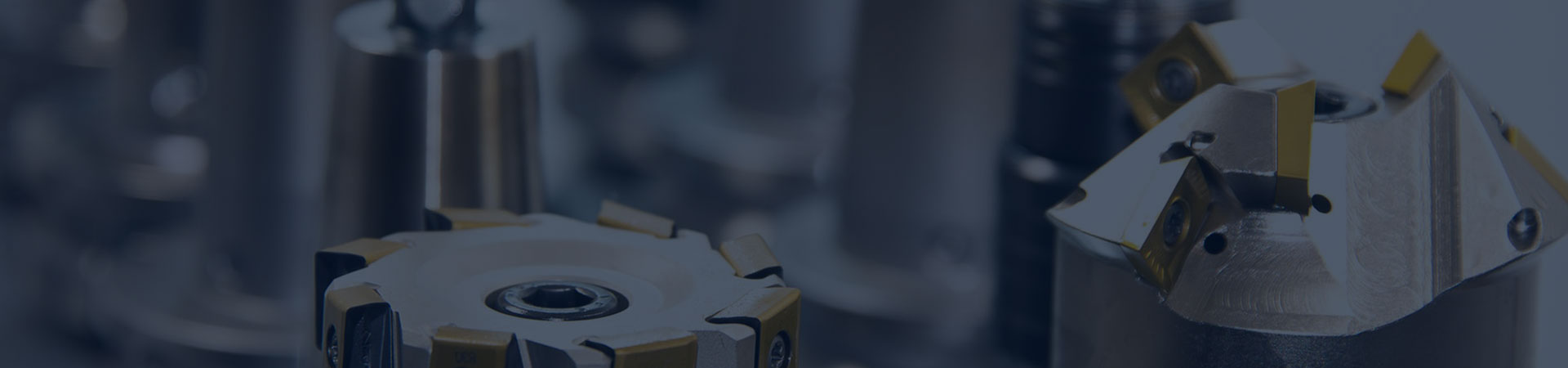
Working principle of marine azimuth thruster
Azimuth thruster, also known as "Z propeller", "rudder propeller", "Z propulsion arrangement", or "all-direction propeller". It refers to a propeller that rotates 360 ° around a vertical axis through the action of umbrella gear devices, worm gear devices, etc. and has two functions: propulsion and manoeuvring of ships. The direction of thrust can be changed arbitrarily with the change of position, making the ship turn around in place and move back and forth freely. Both manoeuvrability and manoeuvrability have been greatly improved. However, due to the large size of the hub, the relative efficiency is low, and the transmission and control mechanisms are also complex, requiring high material performance and process requirements. Therefore, it is mostly used in small and medium-sized engineering and port ships.
The propeller or ducted thruster can rotate 360 ° around the vertical axis in the horizontal plane through the transmission mechanism of the bevel gear system, which is used to propel and manipulate the thruster of the ship.
Overview
Working principle
The output power of the main engine is the vertical shaft through the first-stage umbrella gear and is then transmitted to the thruster through the second-stage umbrella gear, forming a Z transmission system. There is also a hydraulic pump driving the worm gear to drive the entire pusher device to rotate 360 ° horizontally.
The Z-shaped shaft system and guide pipe propeller are all installed on a cylindrical body, and the entire device can be lifted out or installed at the deck opening. The unit horsepower thrust of the azimuth thruster is high, and the manoeuvrability is good. The tugboat equipped with dual rudder propellers can rotate, translate, and reverse on-site. The backward thrust is the same as the forward thrust and can be remotely operated by combining the aircraft. Installing a mesh cover in front of the duct can protect the propeller. The motion state of the azimuth thruster includes two states: steady and unsteady. The steady working state of an azimuth thruster refers to the situation where the pitch angle of the blades does not change during one rotation, and only axial thrust is generated. The unsteady working state of an azimuth thruster refers to the periodic change in the pitch angle of the blade during one rotation of the blade so that the circulation on the blade not only changes radially but also changes with the rotation of the blade. Therefore, there are not only free vortices but also radial vortices in the wake.
Advantage
For the maneuverability of ships during navigation, azimuth thrusters are better than ducted thrusters and flat rotating thrusters. This is because although ducted thrusters have greater thrust when moving forward, they have poorer thrust and less than ideal maneuverability when reversing; On the contrary, a rotary propeller can achieve good maneuverability, but the mechanism is complex, the cost is high, and it is prone to damage; Although the 360 ° rotary thruster does not have a rudder, it can fully convert the thrust of the propeller into a force equivalent to the rudder, which is beneficial for maneuvering the ship. Moreover, the unit power thrust of the 360 ° rotary thruster is large, and the backward thrust and forward thrust are basically the same. Equipping a fully rotating thruster can simplify the shape of the stern of a ship, reduce ship resistance, and in the event of thruster failure, the entire machine can be lifted out of the engine room without the need for docking, greatly simplifying maintenance work and increasing the service life of diesel engines. This new type of thruster is suitable for various engineering ships, such as tugboats, top wheels, floating cranes, dredgers, ferries, and flat-bottomed boats for operations, and has broad market application prospects and military significance.
For more azimuth thruster information, please click here.