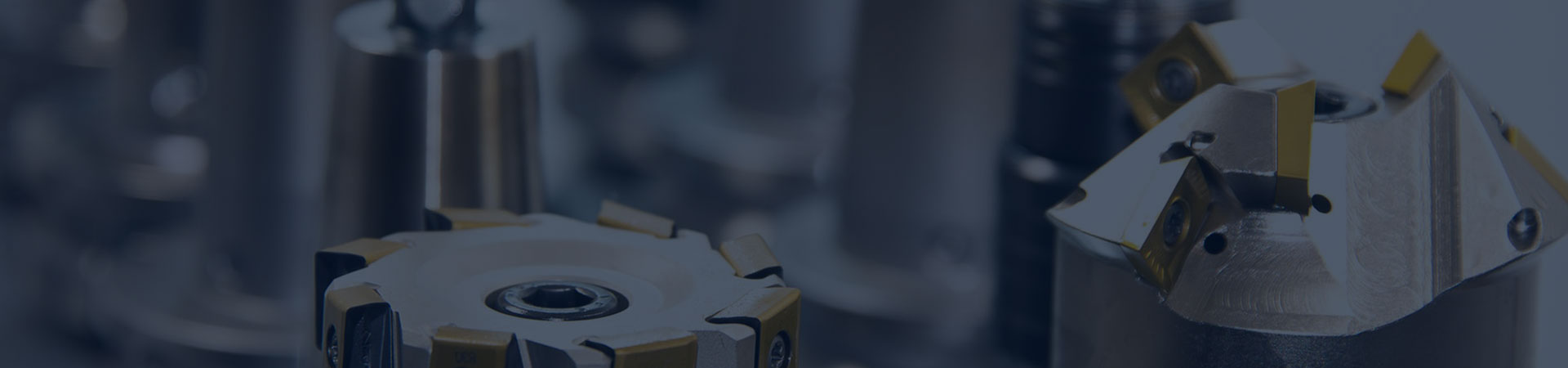
What Type Of Wire Rope Is Used On Cranes
Wire ropes used on cranes typically are required high standards for strength, durability, and flexibility, as they are crucial for lifting and moving heavy loads. The selection of the wire rope for a crane depends on factors such as the crane type (e.g., mobile crane, tower crane), load capacity, lifting height, intended application and environmental conditions. It's essential to choose the appropriate wire rope that meets the specific requirements of the crane's operation to ensure safety and optimal performance. Additionally, regular inspection and maintenance of the wire rope are crucial to ensure safe crane operations.
Overview
Common types of wire ropes used on cranes
6x19 Class Wire Rope
This is a common type of wire rope used in general-purpose crane applications. It consists of 6 strands with 19 wires per strand. It offers good flexibility and resistance to abrasion.
7x19 or 6x37 Class Wire Rope
These are common classifications of wire rope construction. 6x37 class is similar to the 6x19 class but with more wires(37) per strand. These wire ropes offer a good balance of flexibility and strength, making them suitable for various crane applications.
8x19 Class Wire Rope
This type of wire rope has 8 strands with 19 wires per strand. It offers excellent flexibility and is suitable for applications where the rope needs to flex and bend easily.
Rotation-Resistant Wire Rope
Rotation-resistant wire ropes (Spin-Resistant Wire Rope) are designed to minimize twisting and spinning of the load during lifting operations. They are often used in applications where precise load control and minimal rotation are critical, such as in tower cranes, overhead cranes, and some mobile cranes. They are constructed with multiple layers of strands that counteract the tendency to rotate under load.
Non-Rotation-Resistant Wire Rope
Non-rotation-resistant wire ropes are used in applications where rotation is not a significant concern. These ropes are more straightforward in design and construction compared to rotation-resistant ropes. They are often used in applications such as mobile cranes, crawler cranes, and some construction equipment.
4 strand flat no-rotating wire rope
Comprising 4 fan-shaped strands, supported by nylon fibers between the strands, the wires are in linear contact. After being formed, the rope is forged with special equipment, providing a larger contact surface with the pulley and excellent anti-rotation performance.
Compacted strand wire rope
Compacted strand wire rope has higher load-bearing capacity and longer service life compared to regular wire rope, making it suitable for lifting and carrying large and heavy loads.
Galvanized or Stainless Steel Wire Rope
In environments where corrosion is a concern, galvanized or stainless steel wire ropes are used to resist rust and degradation. They are often used in marine and offshore crane applications.
Plastic-Impregnated Wire Rope
These wire ropes have plastic coatings or lubricants that provide additional protection against corrosion and reduce wear. They are suitable for outdoor and marine crane applications.
Crane-Specific Wire Rope Configurations
Some crane manufacturers may specify unique wire rope configurations or types tailored to their crane designs. These may include specialized constructions or coatings to optimize performance and safety.
Precautions when replacing wire ropes on a crane:
The new rope should be of the same type and specification as the original rope. If a different type is used, the new rope should have equal or higher performance than the old rope and should be compatible with the drum and sheave groove shapes.
The lay direction of the wire rope should be consistent with the helical direction of the drum rope groove. When single-layer winding, a guide should be used to prevent the rope from becoming tangled.
When removing the wire rope from the drum or coil, care should be taken to prevent it from looping, twisting, bending, or sticking to foreign objects. When cutting the wire rope, both sides of the cut should be securely tied with fine wire to prevent the rope strands from loosening.
When the wire rope comes into contact with a part of the machine, protective measures should be added to the contact area. When the bundled rope contacts the edges and corners of the lifted object, wooden blocks or copper plates should be added to the corners to prevent the wire rope from being cut.
When lifting heavy objects, the wire rope should not be lifted diagonally to prevent the rope from becoming tangled and causing malfunctions.
Overloading during lifting is strictly prohibited. Overload limiters or torque limiters should be installed, and sudden impacts and vibrations should be avoided as much as possible. A lifting limit switch should also be installed to prevent the wire rope from being pulled off due to overwinding.