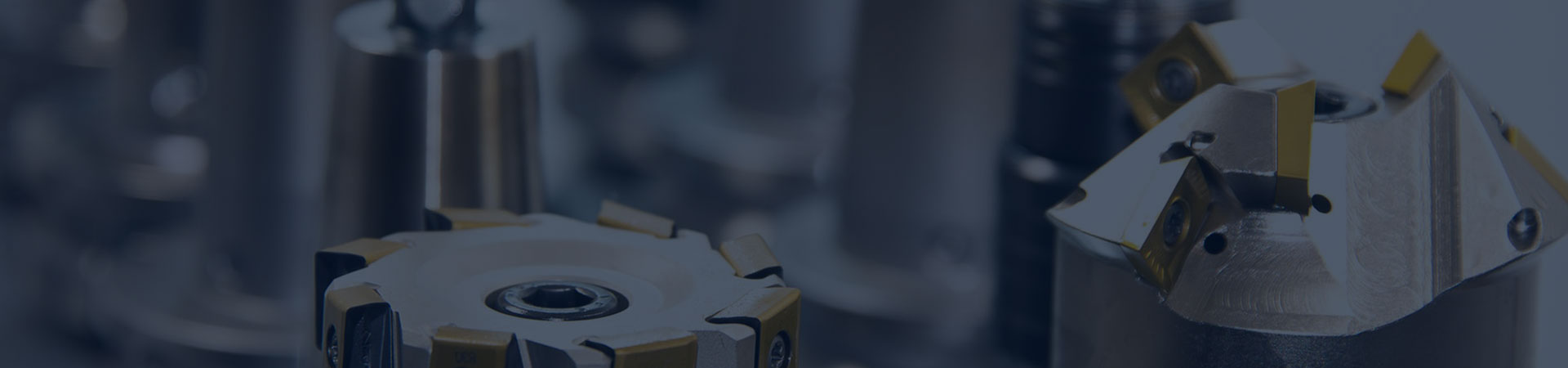
What Is An Elbow?
Pipe fitting elbow (Elbow) is a connector used to change the direction of fluid flow in piping systems, through a specific bending angle (such as 45 °, 90 °, 180 °) to achieve pipe steering.
Core function:
Reduce fluid resistance, reduce pressure loss and turbulence caused by sharp turns.
Avoids stress concentrations and wear and tear on pipes caused by rigid right-angle connections.
Overview
Classification and characteristics of pipe fitting elbow
Classification basis | typology | Features and Typical Uses |
perspectives | 90° elbow | Most commonly, used for right-angle turns (e.g., building fire protection piping). |
45° elbow | Ease steering and reduce pressure drop (e.g. pump inlet and outlet flexible connections). | |
180° elbow (return bend) | U-pipe circulation systems (e.g. chemical reactor cooling circuits). | |
Manufacturing process | Manufacturing process | The surface of hot push elbow is smooth and suitable for thick-walled pipe; the cost of cold forming is low and suitable for small batch production. |
Stamped Elbow | High productivity, but high tooling costs, suitable for standardized sizes (e.g. Sch40 standard wall thickness). | |
connection method | Butt-welding elbow | Preferred for high-pressure pipelines (e.g., oil crackers), which need to be welded to the pipeline and hermetically sealed. |
Threaded elbow | Low-pressure, small-diameter piping (e.g., domestic gas piping) for quick disassembly. | |
special category | Reducing elbow | Connecting pipes of different diameters (e.g. pump reducer connections). |
Flange Elbow | With flange for easy bolting (e.g., removable lines for sewage treatment plants). |
Key manufacturing processes
Hot push molding: medium frequency heating to above 950°C, extrusion molding with mandrel to ensure uniform wall thickness.
Cold stamping: applicable to thin-walled stainless steel elbow, need to control the rebound deformation.
Quality control: ray testing (RT) to detect internal cracks, hardness test to ensure that the material is up to standard.
Material selection guide
material (that sth is made of) | Applicable Scenarios |
Stainless Steel (316L) | Highly corrosive environments (e.g. coastal chemical plants, food processing pipelines). |
Carbon Steel (WPB) | High-temperature and high-pressure steam piping (e.g., thermal power plants) at a lower cost. |
Alloy steel (P91) | Main steam piping for supercritical power stations, resistant to temperatures up to 650°C. |
PVC/CPVC | Chemical acid and alkali media transportation (such as electroplating workshop), drinking water system. |
Frequently Asked Questions
Elbow “long radius” and “short radius” how to choose?
Long radius elbow (R = 1.5D): small pressure drop, suitable for high-flow media (such as main steam piping).
Short radius elbow (R = 1.0D): space-saving, but the pressure drop is large, suitable for restricted sites (such as ships cabin).
How to prevent elbow weld cracking?
Countermeasures: preheat before welding (carbon steel needs 200-250℃), use low hydrogen welding rod (e.g. E7018), heat treatment after welding.
Problems: erosion corrosion (e.g. refinery catalytic cracking unit)
Countermeasure: Lined with tungsten carbide coated elbow, life can be extended by 3 times.
Problem: Welding heat affected zone cracks
Countermeasure: Use ER70S-6 wire, preheat 200-250℃ to reduce hydrogen cracking.