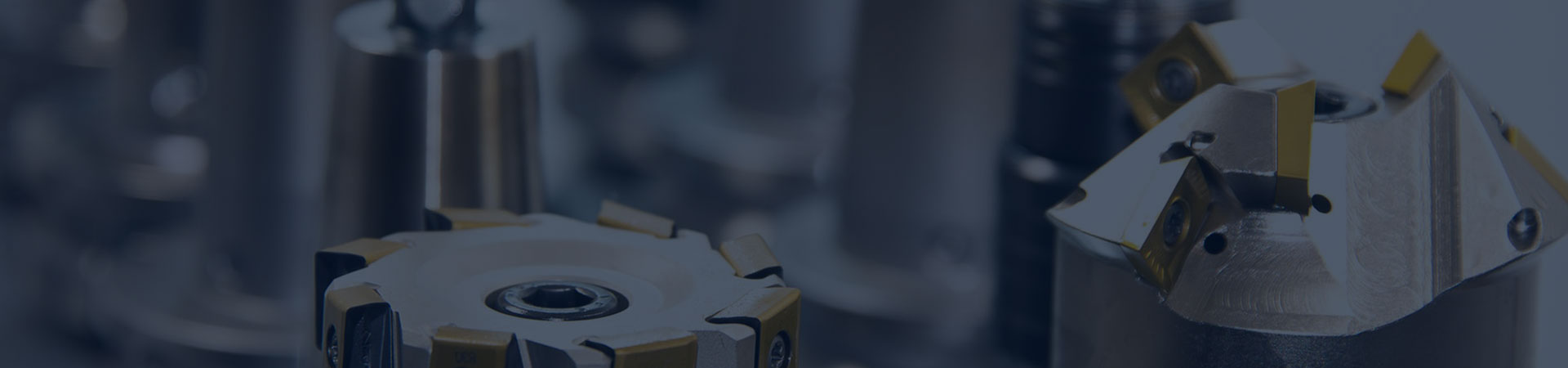
What causes needle valves to fail?
Needle valves have some problems in the long-term use of the process. These include problems with the valve body, spool, sealing surface, etc., and also blocking faults, air leakage faults, valve slippage, inflexible operation and other faults. For different causes of failure, different troubleshooting and maintenance measures are taken to solve the problem in time to ensure the normal operation of the needle valve. Also need to do a good job of routine maintenance and maintenance of needle valve, to extend the service life, improve work efficiency.
Overview
Common Failures:
Valve trim is damaged due to rust, impurities, etc., causing the valve trim to be stuck.
Valve stem jammed; too large or too small gap between valve stem and power mechanism.
Aging and wear of seals; Wear and deformation of valve stem; Damaged surface on sealing surface or sealing ring will affect the sealing effect.
The pipeline contains particulate matter and impurities; the valve has not been used for a long time, and there is a lot of internal precipitation material.
Solutions:
If the needle valve is covered with dirt, we should clean the valve and trim. Clean the valve and remove rust and other dirt, and use polish to clean the valve to restore its smoothness.
If there is a chip or damage on the sealing surface or sealing ring of the valve, it needs to be replaced to ensure the sealing of the valve.
The gears of the sealing gasket are fitted with some fittings. If it is damaged, the gear part can be adjusted and the fittings can be replaced, both to ensure the sealing and to prolong the common effect.
If none of the above methods can solve the problem of the valve not closing tightly, then the whole valve body needs to be replaced.
Picture: