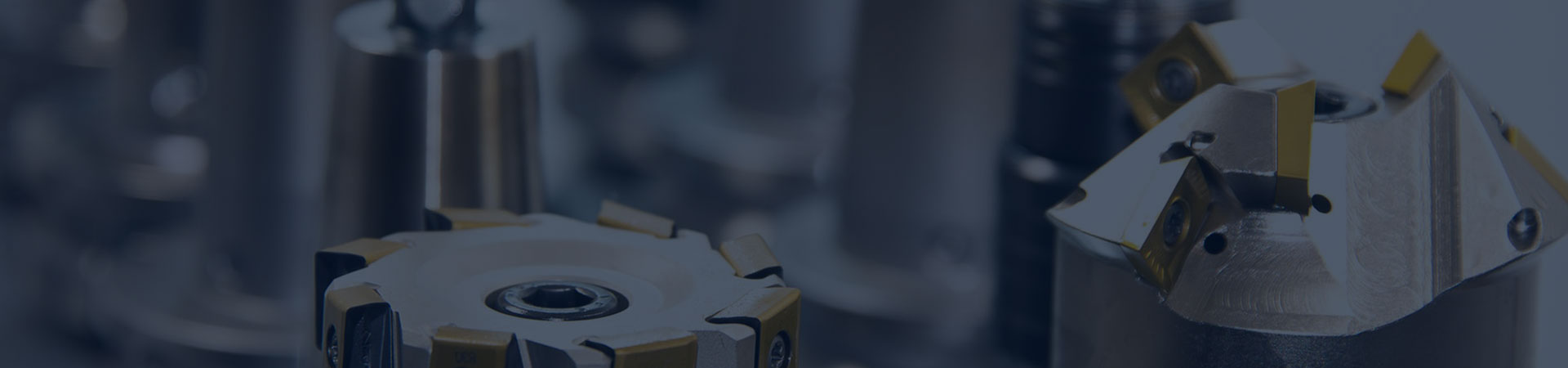
What are the configurations of marine air compressors
Marine air compressors can be directly connected or belt-driven, as well as diesel engine belt-driven. The common base can be equipped with an oil-water separator (gas water separator), pressure controller, unloading solenoid valve, temperature control device, shock absorber, exhaust hose at the air outlet, etc.
The marine air compressor can be equipped with a wall-mounted electric control box, which can achieve automatic unloading, starting, and stopping; Functions such as motor overload, automatic alarm, high-temperature alarm, and shutdown.
Each marine air compressor can have this configuration.
Overview
Marine air compressors are one of the crucial equipment in ship systems, mainly used to provide starting air, control air, and instrument air. In order to ensure its normal and efficient operation, the configuration of the air compressor needs to consider multiple aspects.
Basic configuration:
(1) Compressor body:
Type: It can be reciprocating, screw, centrifugal, etc. Common types are reciprocating and screw.
Drive method: electric motor drive or diesel engine drive.
(2) Electric motor (emergency air compressor with diesel engine):
Specification: Select an appropriate power and voltage level electric motor according to the power requirements of the compressor.
Start method: direct start or star delta start.
(3) Control system:
Automatic controller: used to automatically start, stop, and monitor the operating status of the compressor.
Display: displays parameters such as pressure, temperature, and operating status.
Alarm system: issues an alarm in the event of an abnormal situation.
Auxiliary configuration
(1) Air filter:
Inlet filter: filters the air entering the compressor to prevent impurities from entering the interior of the compressor.
Export filter: Filter the compressed air to ensure the cleanliness of the output air.
(2) Air cooler:
Intercooler: In a multi-stage compressor, it cools the air between each stage.
After cooler: cools the final output compressed air and lowers the air temperature.
(3) Oil water separator:
Function: Separate oil and water from compressed air to ensure air cleanliness.
(4) Air storage tank:
Function: Store compressed air, balance gas supply pressure, and reduce compressor start-up frequency.
Specification: Select an appropriate capacity and pressure level air storage tank according to system requirements.
(5) Safety valve:
Function: Release excess air when the pressure exceeds the set value, protecting system safety.
(6) Pressure switches and sensors:
Function: Monitor system pressure and control the start and stop of the compressor.
Other configurations
(1) Condenser:
Function: Condensing water vapor in compressed air, reducing the impact of moisture on the system.
(2) Drainage device:
Automatic drain: Automatically discharge condensate water to keep the system dry.
Manual drain: Manually operate the drain and regularly drain the condensate in the system.
(3) Lubrication system:
Oil lubrication system: ensures lubrication of internal components of the compressor and reduces wear.
Oil level indicator: displays the level of lubricating oil to ensure sufficient lubrication.
(4) Electrical control cabinet:
Function: Centralized control and protection of electrical equipment, convenient operation and maintenance.
(5) Noise control device:
Silencer: reduces noise during compressor operation and improves ship comfort.
(6) Anti vibration foundation:
Function: Reduce vibration during compressor operation, protect ship structure and other equipment.
For more marine air compressor information, please click here.