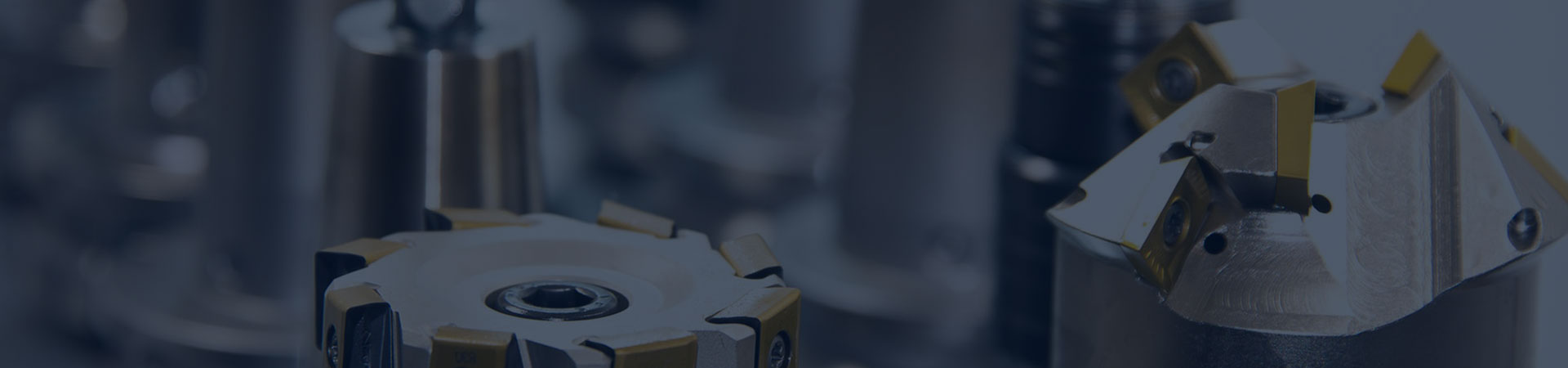
Welding procedure assessment of marine propellers
The welding procedure for copper alloy propeller should comply with ISO standards and is to be subject to approval by relevant classification societies. The approval is a general approval according to different materials, welding method, welding position, welding grooves, preheating and welding conditions (including stress relief heat treatment). The approval is essential for the propeller manufacturer. The approval is not for specific defects of specific propeller, but for butt weld test specimen to check technical conditions of the manufacturer.
Overview
The following is based on CCS standards:
The test specimens for approval are two piece of down-hand and butt-weld specimens of which minimum length is 300mm and minimum width is 150mm and minimum thickness is 30mm, as shown in the following figure(1):
The preparation of tensile test specimen is as shown in the following figure (2).
The tensile strength of two test specimens is to comply with the requirements in the following Table (1):
Macro-etching: The corrosive liquid for the three macro-etch specimens are to be prepared according to the following proportion:
Ferric trichloride 5g
Hydrochloric acid 30ml
Water 100ml
The macro-etch specimens are to be free from cracks,lack of fusion or blowholes exceeding 3mmor slag inclusions.
Non-destructive test: after welding, the welded area is to be subject to dye penetrate and radiographic testing. No cracks or open voids exceeding 3mm are permitted in dye penetrate test.Imperfections detected by liquid penetrant testing are to be assessed in accordance with Section 4, Chapter 8 of PART THREE of CCS Rules for Materials and Welding. Radiographic test is to be carried out referring to the standard on class II of aluminum pressure vessels in JB4730-2005. Thisregulation is not to exclude the adoption of subsequent national or industry standards on ultrasonic testing and radiographic testing.
Welding procedure: in the development of welding procedure, Table 8(3) and Table 8(4) may be used as a guidance to select consumables and determine pre-heating temperature, interpass temperature, post-weld heat treatment temperature and time.
Re-testing: Where the result to tensile test of any specimen is unacceptable, duplicate test specimens of the same type are to be prepared from the original welded assembly or from a new assembly welded with the same procedure and using welding consumables from the same batch, and the results of all re-tests are to be satisfactory.
Test record: Welding conditions for test assemblies and test results are to be recorded in weldingprocedure qualification record. Forms of welding procedure qualification records can be takenfrom the Society’s rules or from relevant standards. A statement of the results of assessing each test piece, including repeat tests, is tube made for each welding procedure qualification records. The relevant items listed for the WPS are to be included. The welding procedure qualification record is to be signed by the Surveyor witnessing the test and is to include the Society´s identification.
Range of approval
General: All the conditions of validity stated below are to be met independently of each other. Changes outside of the ranges specified are to require a new welding procedure test. A qualification of a WPS obtained by a manufacturer is valid for welding in workshops or sitesunder the same technical and quality control of that manufacturer.
Base metal: The range of qualification related to base metal is given in Table (2)
Thickness: The qualification of a WPS carried out on a weld assembly of thickness t is valid for the thickness range given in Table (3)
Welding position: Approval for a test made in any position is restricted to that position.
Welding process: The approval is only valid for the welding process used in the welding procedure test. Single run is not qualified by multi-run butt weld test used in this UR.
Filler metal: The approval is only valid for the filler metal used in the welding procedure test.
Heat input: The upper limit of heat input approved is 25% greater than that used in welding the test piece. The lower limit of heat input approved is 25% lower than that used in welding the test piece.
Preheating and interpass temperature: The minimum preheating temperature is not to be less than that used in the qualification test. The maximum interpass temperature is not to be higher than that used in the qualification test.
Post-weld heat treatment: The heat treatment used in the qualification test is to be specified in pWPS. Soaking time may be adjusted as a function of thickness.
For more marine propeller information, kindly please click here.