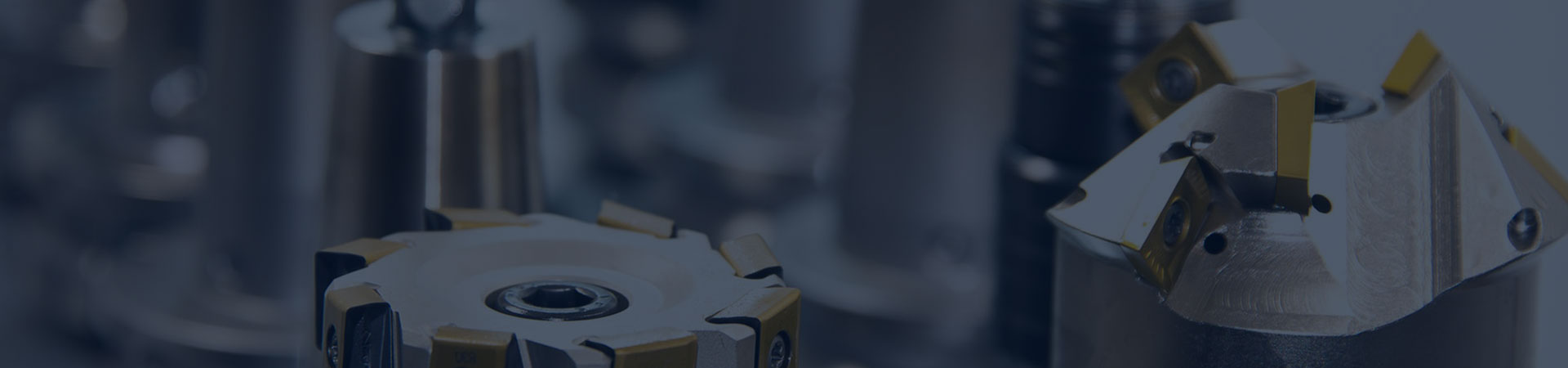
Unit or batch inspection of marine propeller
The quality inspection of marine propellers is usually divided into unit or batch inspection and batch inspection. Unit or batch inspection is mainly applicable to the following situations:
Customized propellers: Each propeller is customized according to the specific needs of a particular vessel, typically used for large or special-purpose vessels.
High-value propellers: Due to their high value, strict quality control is required for each propeller.
Special materials or processes: Propellers manufactured using special materials or processes may require more detailed testing.
Overview
The following test requirements are based on CCS standards:
1 Each propeller and its components are to be subject to test in accordance with CCS Rules. The tests such as chemical composition, metallographic structure(for Cu1 and Cu2), mechanical properties, appearance (including surface roughness), size, dimensional tolerance, NDT, static balancing, dynamic balancing (if applicable), pressure (if applicable) and weighingare to comply
with the requirements ofCCS Rules and the drawings approved by CCS.When the propeller intend to use in the ship not surveyed by CCS is applied to be surveyed by the Society, strength calculation for the propeller based on the rated power of main engine of the ship and the running speed of the propeller at rated power of main engine(or the rated running speed of main engine and gear box deceleration ratio) should be carried out with satisfaction according to CCS Rules for Classification of Sea-going Steel Ships or CCS Rules for Construction of Inland Waterways Steel Ships by the manufacturer. The strength calculation for the propeller with the drawings of the propeller should be submitted to CCS by the manufacturer.
2 size, dimensional tolerance, static balancing, dynamic balancing (if applicable), and pressure (if applicable ) tests and weighing are to be carried out in accordance with (4), (6), (7), (8) and (9) of this Chapter.
3 The chemical composition analysis report and metallographic structure report should be submitted by the manufacturer to the Surveyor for review. If there is any suspicious, the Society surveyor may check up by sampling.
4 The weighing test may be witnessed by the Surveyor as he requires. The mass difference between left-handed propeller and right-handed propeller in the same ship is not to be greater than 2% of the theoretical mass according to three dimensional model calculation.The NDT of zone A of propeller is to be carried-out in the presence of the Surveyor. For NDT of zones B and C, the manufacturer may submit test report to the Surveyor for review.
5 The inspect record or report on size and dimensional tolerance and surface roughness should be submitted to the society surveyor for review by the manufacturer. If there is a doubt, the surveyor may spot check these datum.
6 Static balancing test of all propeller should be witness by the society surveyor .
7 For propellers running above 500 rpm, dynamic balancing test should be carried out in the presence of the surveyor. F
8 The items except for those specified above are to be carried out in the presence of the Surveyor. For built-up propellers with hydraulic fluid cylinders, the test pressure of each component is to be 1.5 times the design working pressure in approved drawings and a tightness test is to be carried out after installation onboard ships with 1.25 times the design working pressure.
9 After inspection, the manufacturer is to submit quality certificate to the Surveyor for review and as a basis for issue of a certificate of products. The quality certificate is to contain:
(1) Name of the purchaser and order number;
(2) Vessel identification (if known);
(3) Drawing number of propeller;
(4) Diameter, number of blades, pitch, direction of turning;
(5) Heat number, alloy type and chemical composition;
(6) Cast number;
(7) Final mass;
(8) NDT methods and result;
(9) Proportion of α phase (only applicable to Cu1 and Cu2);
(10) Results of the mechanical tests
(11) Castings number;
(12) Skew angle for large skew propellers;
(13) Angle of rake;
(14) Static balancing test report;
(15) Dynamic balancing test report (if applicable);
(16) Pressure test report (if applicable);
(17) Measurement report;
(18) Welding repair record with the photograph(s) of the defect(s) location prior to welding (if no welding operation to all surface of propeller during the whole manufacturing, “No welding” should be remarked in the record).
10 Identification and certification
After survey, each propeller and its components are to be marked by the manufacturer with the following items. For solid propeller, the items are to be marked on the turning face near the small end face of boss and between the two blades.
(1) Grade of cast material or corresponding abbreviated designation;
(2) Identification of the manufacturer;
(3) Heat number, casting number or other marking which will enable the full history of the
casting to be traced;
(4) Date of final inspection;
(5) CCS certificate number;
(6) Ice class notation, if applicable;
(7) Skew angle for high skew propellers;
(8) CCS stamp for accepted castings;
(9) Mass;
(10) For build-up propellers, in addition to the above items on the surface of the boss, the fillet area of blades are to be marked with serial number of blades and spare blades are to be marked with “BY”. Two digits are to be marked on the end face of blade anchor nut and bolt, the first number being thatfor blade and the second that for nut or bolt.
Whether it is unit or batch inspection, it is necessary to follow relevant international and national standards, such as ISO 484, ISO 1940, IMO specifications, etc. At the same time, classification societies such as DNV, ABS, LR, CCS, etc. also have corresponding inspection requirements and certification processes to ensure that propellers meet the requirements of ship design and operation.
Through these strict inspection processes, the quality and reliability of marine propellers in the design, manufacturing, and use process can be ensured, thereby guaranteeing the safe and efficient operation of ships.
For more marine propeller information, kindly please click here.