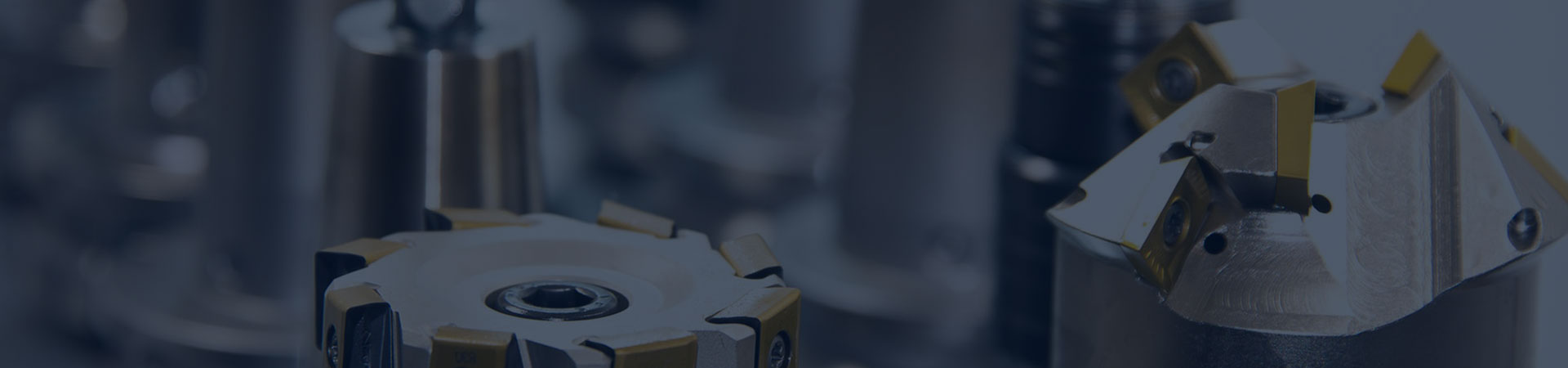
Test requirements for marine air receiver
The test requirements for marine air receiver aim to ensure their safety and reliability in practical use.
The tests of marine air receiver mainly include: Type test and Unit/batch inspection.
Pressure test: Apply water pressure exceeding the working pressure (usually 1.5 times the working pressure) to the air receiver, maintain it for a certain period (usually 30 minutes), and check if there is any leakage or deformation in the air receiver. Conduct air pressure tests when necessary, using compressed air for testing to check sealing.
Air tightness test: Fill the air bottle with compressed air or inert gas to check for leaks. Soap water or specialized airtightness testing instruments can be used for testing.
Safety valve testing: check the safety valve installed on the air receiver to ensure that it can open and close normally under the set pressure.
......
Overview
I. Type test
1 Selection of typical samples
1.1 The air receivers used in type test must be manufactured under supervision of the Surveyor according to the welding procedures and plans approved by CCS, capable of representing or covering the series of air receivers (to be selected according to design pressure, wall thickness of boiler shell, internal diameter, height, and welding procedures of air receivers) within the requested approval scope in respect of performance, characteristics and manufacturing quality.
One or two air receivers are to be taken for each type.
1.2 Welding base metal, joint type, welding consumables, welding methods and welding positions used in welding procedure approval test are to be consistent with welding procedure specifications.
1.3 For marine air receivers used in type test, acceptance of raw materials, main manufacturing processes, inspections and tests, and transfer of relevant marks are to be carried out under supervision of the Surveyor on site. The results are to comply with the requirements of CCS Rules for Classification of Sea-going Steel Ships and approved plans.
2 Type test items and requirements
2.1 Raw material inspection:
Steel plates, steel pipes and welding consumables used in construction of marine air receivers are to be furnished with products certificates issued by CCS or equivalent documents, and their types, grades and specifications are to be consistent with approved plans. The steel plates and steel pipes not having CCS products certificates are to be manufactured at manufacturers accepted by CCS and subject to CCS inspection.
2.2 Visual examination and dimension examination:
(1) visual examination: Misalignment, edge bevel and weld size of butt welds (width and reinforced dimensions of welds) are to be measured, and the results are to comply with the requirements of CCS Rules for Materials and Welding and approved plans. Visually examined boiler shell and end plate are to be free from cracks, scabs and other defects impairing the performance of the products;
(2) dimension examination: Main dimensions such as overall length, overall height, diameter and out-of-roundness of boiler shell are to comply with the requirements of CCS Rules for Classification of Sea-going Steel Ships and approved plans.
2.3 Non-destructive testing
Welds and test plates are to be subjected to non-destructive testing. The method, number and location of the testing are to comply with the relevant requirements in Section 5, Chapter 7, PART THREE of CCS Rules for Materials and Welding. Non-destructive testing acceptance criteria are to meet the following requirements:
Radiographic testing: NB/T47013- II or GB3323- II;
Ultrasonic testing: NB/T47013- I;
Magnetic particle testing: NB/T47013- I;
Penetrant testing: NB/T47013- I.
When using other national or regional standards, to be evaluated by CCS and confirmed the determination level before use.
2.4 Test of welded test plates (air receivers with grade III may be exempted from the test):
The relevant requirements in Section 2, Chapter 7, PART THREE of CCS Rules for Materials and Welding are to be complied with.
2.5 Hydraulic test
The body and standpipe of air receiver are to be subjected to hydraulic test after completion of assembly. The test pressure is to comply with the relevant requirements in Section 5, Chapter 6, PART THREE of CCS Rules for Classification of Sea-going Steel Ships.
2.6 Tightness test
The tightness test of air receiver body can be carried out only after satisfactory hydraulic test and completion of assembly of mountings and fittings. The test pressure is to be working pressure, and the test medium may be air, nitrogen or any other inert gas. The pressure is to be maintained for at least 5 min and no leakage is allowed. If the gastightness test is not practical, the hydraulic test may be accepted in lieu of the gastightness test and the test pressure is to be 1.25 times the design pressure. Test methods and acceptance criteria are the same as those for the hydraulic test.
2.7 Fuse plug test (if any)
Two fuse plugs are to be taken for each specification and subjected to the extrusion resistance testand the test for determination of actuation temperature of fuse plugs. The compressed air is to be applied on the side where the test sample contacts the medium inside the air receiver at the design pressure and temperature of 50 – 60℃ for 2 h. Then the other side is to be examined and no leakage or visible extruded fusible alloy is allowed. After satisfactory results are obtained, the test for determination of actuation temperature of fuse plugs is to be carried out. In general, the actuation temperature of fuse plugs is 100℃.
2.8 Safety valve test (if any)
The test is to cover opening pressure, return pressure, gastightness. The opening pressure is to be more than working pressure and less than design pressure, the return pressure to be not less than 0.85 times the working pressure, and the gastightness test pressure is to be working pressure. No leakage is allowed. The discharge of the safety valve is to be such that the pressure inside the air receiver will not exceed 110% of the design pressure when the outlet valve is closed.
II. Unit/batch inspection
1 Unit/batch inspection for issuing marine products certificates is to be carried out after CCS works approval, unless special consideration is given. Each marine air receiver is to be subjected to unit/batch inspection. Where air receivers are not approved, the unit/batch inspection is to be carried out according to type test requirements.
2 The unit/batch inspection after approval by CCS is to be carried out according to the approved inspection plan, including the following test items:
(1) raw material inspection or retesting;
(2) visual examination and dimension examination;
(3) welding inspection: Inspection prior to welding, welding inspection and visual examination
of welds;
(4) non-destructive testing;
(5) test of mechanical properties of welded test plates (if applicable);
(6) hydraulic test;
(7) tightness test;
(8) safety valve test;
(9) other tests (if applicable).
For more marine air compressor information, please click here.