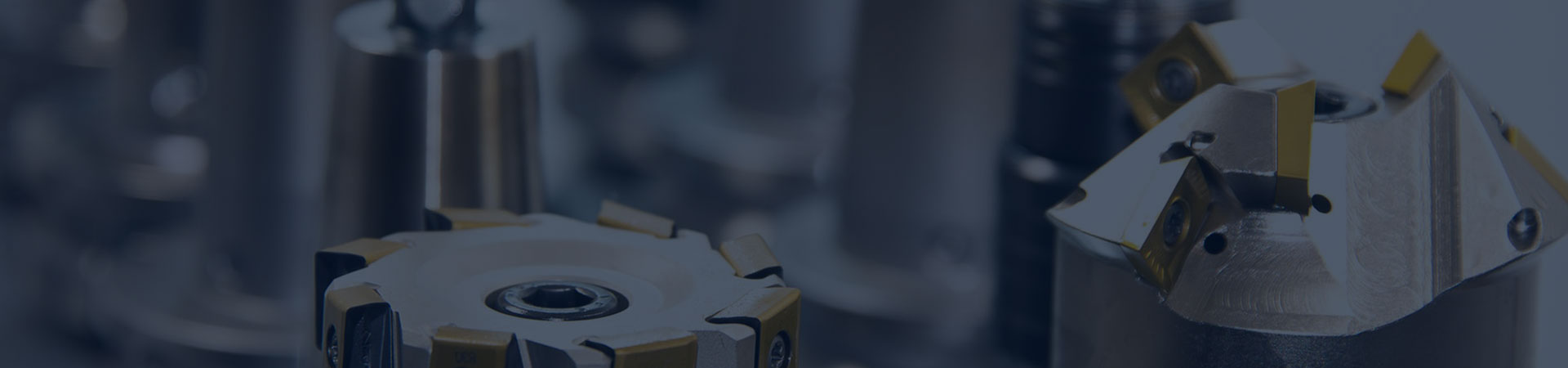
Test for marine air compressors
Conducting tests on marine air compressors requires ensuring their performance, safety, and reliability.
The tests of marine air compressors mainly include: Type test and Unit/batch inspection
Overview
1. Type test
1.1 Selection of typical sample
The test sample for test approval is to be representative of the processing capability and manufacturing level of the works and selected respectively according to the cooling means of the series of products applying for approval and the maximum nominal volume flow under the rated discharge pressure.
1.2 Type test items are to include:
1.3 Type test methods and requirements
1.3.1 Visual inspection
The outside casting and welding surfaces of air compressor are to be cleaned completely without rust, stain or welding slag. The painting surface is to be flat and smooth with uniform color. The paint is to be able to protect against corrosion of salt mist and condensation. The shields of exposed moving parts are to be secure and stable. The heat insulation measures for exhaust pipes under high temperature are to be effective.
1.3.2 Test of main parts materials
For the main parts of air compressor such as crankshaft, connecting rod, rotor, body and gear, at least 2 ~ 3 parts are to be selected for the raw material test in order to verify the parts meet the specified requirements of plans and technical documents.
1.3.3 Pressure and tightness tests of main pressure-bearing parts
The parts under air pressure (e.g. cylinder, piston, cylinder liner, cooler, air-liquid separator, air pipe, housing, exhaust end cover, exhaust chamber, oil pump housing, etc.) are to be able to be subjected to hydrostatic tests to a pressure 1.5 times the maximum working pressure. The hydrostatic test pressure of water channel and water chamber is to be generally 0.50 MPa. The test is to last for 30 min. No leakage is to be allowed during the test.
The connections between parts under air pressure are to be subjected to tightness tests under the maximum working pressure. The test is to last for 10 min. No leakage is to be allowed during the test.
1.3.4 Dynamic balance test of rotor of screw air compressor
The rotor of air compressor is to be subjected to a dynamic balance test. The permissible offset per unit mass of rotor is to meet the specified requirements of approved plans.
1.3.5 Adjustment test and safety valve test
Each air compressor may be subjected to an adjustment test after the running-in period. The air compressor is to operate under the rated condition during the adjustment test. The vibration, air, cooling water and lubricating oil are to be checked for leakage or other abnormalities. The test is to last for at least 30 min. The temperature and pressure of air, water and oil are to be recorded.
The outlet shut-off valve is to be adjusted to make the pressure of air compressor steadily rise. Then the safety valve of air compressor is to be adjusted one by one (the inter-stage safety valve may be adjusted at the final stage) to make the safety valve open at the set pressure. The number of adjustment is not to be less than three times. The result is to be in accordance with the following provisions: The set pressure of inter-stage safety valve is not to be more than 1.2 times the maximum working pressure of the stage. The set pressure of safety valve at final stage is not to be more than 1.1 times the rated discharge pressure.
1.3.6 Test of automatic control and safety alarm device
Automatic control and safety alarm devices of air compressor are to be tested item by item according to the provisions of approved technical documents. The safety alarm device may be tested by simulation.
1.3.7 Measurement of volume flow
(1) Generally, the volume flow is to be measured with such measuring devices as “ISA1932 nozzle and deflector”, “ASME nozzle” or “Arc Venturi nozzle”. When those measuring methods are not appropriate, the “tank-filling method”, “bottle-weighing method” and “flow meter measuring method” may be used with the consent of the Surveyor.
(2) The volume flow measured is not to be lower than 95% of the nominal volume flow when the air compressor operates under the rated condition.
1.3.8 Measurement of shaft power
The shaft power of air compressor may be measured by the following methods:
(1) Directly measure the input torque and speed of compressor shaft with a tacho-torquemeter or a DC dynamometer;
(2) Measure the output power of motor with a calibrated direct-current motor, and then multiply the output power by the transmission efficiency;
(3) Indirectly measure the output power of motor by the loss analysis method, and then multiply the output power by the transmission efficiency;
(4) The measured value of the shaft power of air compressor is to be less than the specified numerical value.
1.3.9 Measurement of vibration
The vibration is to be measured when the air compressor operates under the rated condition. The vibration intensity is to meet the requirements of this Guideline. For the piston air compressor, the vibration measuring points are crankshaft and end cover of each stage. For the screw air compressor, the vibration measuring points are spindle and front and rear bearing blocks. Each measuring point is to be respectively measured in three directions.
1.3.10 Durability test
(1) The air compressor applying for approval to CCS is to be subjected to a durability test according to the specifications of the table below:
(2) The test is to be conducted under the rated condition. The volume flow of air compressor is to be measured when the test starts and ends. The flow is not to be reduced by more than 10%. The temperature and pressure of oil and water are to be measured every 10 h.
(3) The air compressor is to be subjected to teardown inspection after the test. All parts are to meet the specified requirements.
1.3.11 Environment adaptation test
The air compressor applying for approval to CCS is to be subjected to the tests below:
1.4 Determination and exemption of the test items
All applicable test items in Article 8.3 are to be generally performed for the first approval. The applicant may apply for exemption of partial test items in written form provided that the following conditions are met. Considerations are to be paid by CCS according to the production status, production history and usage records of products, etc.
(1) The applicant is able to provide the test report of appropriate test items issued by a recognized technical authority in recent period (within a year);
(2) The applicant is able to provide the test reports of appropriate test items signed by IACS members.
1. Unit/batch inspection
2.1 After obtaining type approval from CCS, the marine air compressor produced by the works in accordance with the approved conditions (including assembly, process, etc.) may be installed on board after passing the unit/batch inspection by CCS.
2.2 For approved products, the manufacturing works is to test each product according to items 1 ~ 8 listed in Table 2.2 and to submit a test report to the Surveyor of CCS for review. The Surveyor is to randomly take samples at a proportion of 10% for each specification of products applying for inspection. A certificate is to be issued once the product passes the inspection.
For more marine air compressor information, please click here.