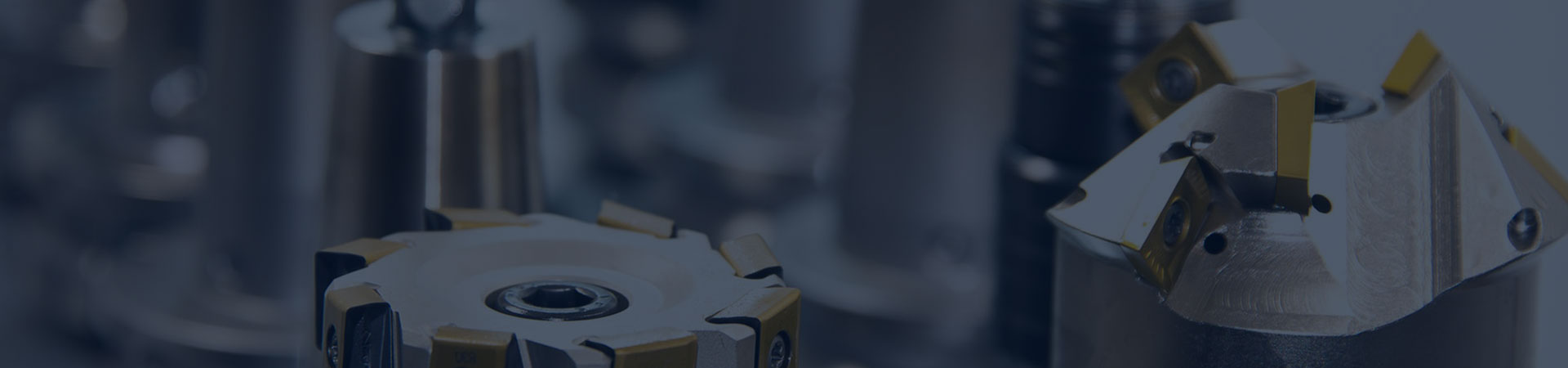
Solid Socket Welding Flange
Solid Socket Welding Flange is a flange where the end of the pipe is inserted into the flange ring step and welded at the end and outside of the pipe. There are two kinds of flanges with and without neck. Necked pipe flanges have good rigidity, small welding deformation, better sealing, and can be used for pressure of 1.0~10.0MPa. B-type flanges for containers are also socket weld flanges, which are used in occasions with high sealing requirements. When designing, socket weld flanges can be calibrated as integral flanges.
Overview
Welding Method:
Socket welded flanges are mainly welded together by inserting the pipe into the flange. This welding method involves inserting one end of the pipe into the bore of the flange and then welding at the inserted portion to ensure a strong connection between the pipe and the flange.
Socket welding is usually used for smaller pipe sizes, such as carbon and stainless steel pipes up to 2 inches, while butt welding is usually used for materials such as titanium pipes, duplex steels, and nickel-based alloys.
During the operation, it is necessary to ensure that the pipes and flanges are clean and free from oil, dust and water to ensure the quality of the weld. In addition, socket welded joints usually cannot be X-ray detected, so special attention needs to be paid to their inspection and maintenance in practical application.
Drawing:
Picture: