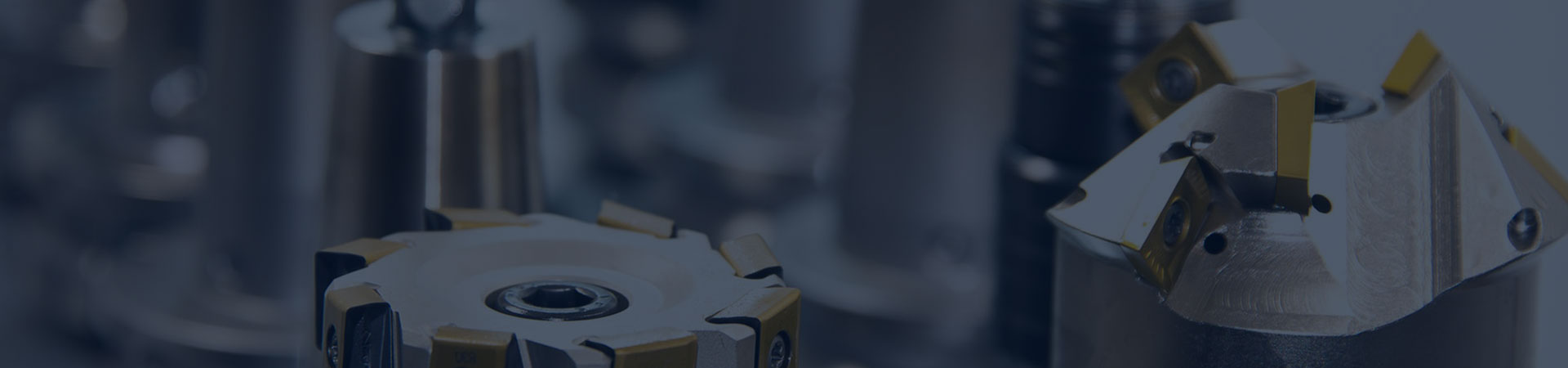
Process requirements for marine air compressors
Marine air compressors are used to provide compressed air for various systems in ships.
The rated pressure and rated displacement should meet the corresponding usage requirements.
The actual weight deviation between the piston, connecting rod, and balance iron and the weight shown on the drawing should not exceed the specified value.
To make it easy to reset the air compressor and prime mover after disassembly, positioning pins should be used between the prime mover and the common base.
Pressure bearing components of air and cooling water should undergo hydraulic pressure testing. The air chambers and pistons of cylinders, siphon covers, coolers, liquid gas separators, etc. should be subjected to a water pressure test at 1.5 times the rated working pressure; The water pressure test pressure of the cooling water circuit is 0.5MPa, and various water pressure tests are conducted for 30 minutes without leakage.
Overview
Process requirements
1. The actual weight of the piston, connecting rod, and balance iron should not deviate from the weight shown on the drawing by more than the following provisions:
Pistons: ± 5%
Connecting rod: ± 5%
Balance iron: ± 4%
The flywheel (pulley) should undergo static balance correction.
2. When the air compressor and the prime mover are directly connected using elastic couplings, the alignment requirements of the two machine spindles should comply with the provisions in Table 5.
1. To make it easy to reset the air compressor and prime mover after disassembly, positioning pins should be used between the prime mover and the common base.
4. Pressure bearing components of air and cooling water should undergo hydraulic pressure testing. The air chambers and pistons of cylinders, siphon covers, coolers, liquid gas separators, etc. should be subjected to a water pressure test at 1.5 times the rated working pressure; The water pressure test pressure of the cooling water circuit is 0.5MPa, and various water pressure tests are conducted for 30 minutes without leakage.
Safety and environmental protection requirements
1. The safety valve of the air compressor should operate flexibly and be safe and reliable. When the exhaust control valve is fully closed and the exhaust pressure of the air compressor rises to 110% of the rated exhaust pressure, the final stage safety valve opens. At this time, the exhaust pressure no longer rises, and the jumping pressure of the inter stage safety valve should not exceed 120% of the rated exhaust pressure of that stage.
The rupture of the safety film on the cooling water chamber or the jumping pressure of the safety valve is 0.4-0.45MPa.
3. An intake silencer filter should be installed at the intake port of the air compressor.
4. The air compressor unit is installed on the test bench of the manufacturing plant and operates under rated conditions with a vibration intensity value of Vrms ≤ 18mm/s.
5. The driving and transmission devices should be equipped with protective covers mainly made of metal wire mesh or steel plates.
Appearance requirements
1. The casting, welding, and processing surfaces on the outer surface of the air compressor should be cleaned and scraped without rust, scale, or welding slag. The painted surface should be flat, smooth, and of consistent color. Fastener operating parts should be decorated, and the paint should be able to prevent corrosion from salt mist, oil mist, and moisture. Putty is not allowed on the outer surface of the cylinder and cylinder head of the air-cooled air compressor. It should be sprayed with thermal conductive paint (such as silver powder paint) with good thermal conductivity.
2. The air pipe, water pipe, and oil pipe of the air compressor should be painted according to the color specified in GB 3033 to indicate the purpose of the pipeline.
3. Exposed fasteners and operating components should undergo decorative treatment (such as blueing or chrome plating).
4. The manufacturer guarantees that the paint on the air compressor will not peel off or turn yellow within 12 months after delivery, provided that the user complies with the usage rules.
For more marine air compressor information, please click here.