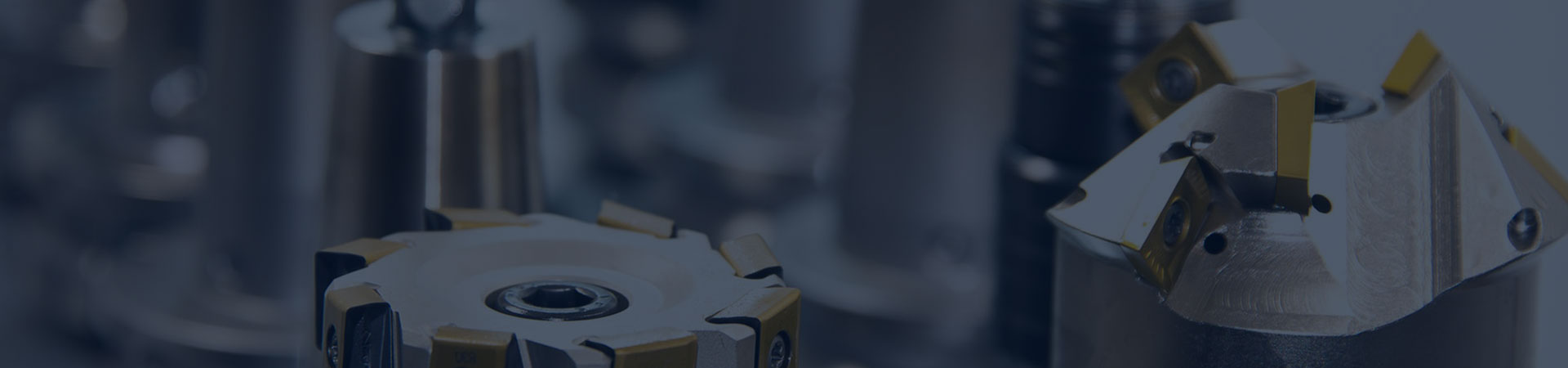
Polymer bearings used in marine shaft systems
The application of polymer bearings in marine shaft systems is very important because they provide many advantages that traditional metal bearings cannot match.
The use of these bearings not only improves the operational efficiency of ships, but also reduces maintenance costs and downtime.
The application of polymer bearings in marine shaft systems not only improves the performance and reliability of the shaft system, but also enhances the overall performance and economic benefits of ships.
This makes polymer bearings an indispensable part of modern shipbuilding and maintenance.
Overview
Application
The main application areas of polymer bearings in marine shaft systems include:
Propeller bearings: support and guide the rotation of the propeller shaft to ensure smooth operation.
Tail shaft bearing: used to support the tail shaft and ensure its stability during the transmission process.
Intermediate bearing: used to support and guide the intermediate shaft in the ship's transmission system.
Advantage and features
Corrosion resistance: Polymer materials have extremely high resistance to seawater and other corrosive media, reducing the corrosion problem of bearings in marine environments.
Self lubrication: No additional lubricant required, it has good lubrication performance and reduces maintenance requirements.
Low friction coefficient: The low friction characteristics of polymer materials reduce energy loss and improve transmission efficiency.
Lightweight: reduces the overall weight of the ship, improves navigation performance and fuel efficiency.
Shock absorption and noise reduction: Good shock absorption and noise reduction performance improves the smoothness and comfort of ship operation.
Performance technical parameters
Mechanical properties: tensile strength ≥ 50MPa
Compression strength ≥ 100MPa
Bending strength ≥ 30Mpa
Hardness ≥ Shore A90
Physical properties: Linear expansion coefficient 7.8 × 10-5 ℃ -1
Volume water expansion rate < 1.5%
Friction and wear performance: Dry sliding friction coefficient < 0.03
Specific wear rate < 8.0 × 10-7mg/N.m
The friction coefficient under artificial seawater is less than 0.08
Specific wear rate < 3.0 × 10-6mg/N.m
Corrosion performance: After soaking in artificial seawater for 10 days, the retention rate of bending strength is ≥ 65%
Dimensional design
1. Length to diameter ratio (L: D)
For water lubricated stern shaft systems, the typical ratio is 3:1;
For water lubricated rudder systems, the typical ratio should be 2:1.
2. The recommended wall thickness (T) is T (mm)=0.06d (mm)+2mm, where d is the journal.
3. Outer diameter and inner diameter
Outer diameter: The maximum inner diameter of the shell plus interference.
Inner diameter: maximum shaft diameter plus 1.2 times interference and running clearance.
Wall thickness: Actual trial has proven that the optimal wall thickness is calculated using the following formula.
T=0.5 [Shell inner diameter - d (basic shaft diameter) - (0.2 x interference) - Running clearance]
4. Interference and running clearance
The running clearance is calculated according to the following formula
Running clearance (mm)=(k+0.0016d) x 2 (shaft diameter mm)
Operating conditions
1. Water lubrication: The size and flow rate of the water lubrication stern shaft sand axial water tank are shown in the table below. The sink is evenly distributed. There is no slot at the 6 o'clock position. The inner diameter water tank of the water lubricated stern bearing is rectangular, and its size can also be designed according to the following formula.
Maximum groove depth g=0.33T (T is the recommended optimal wall thickness)
Slot width W=1.5g
Chamfer r=0.33g
2. Oil lubrication: The oil lubricated stern bearing does not require axial slotting, only two arc-shaped indentations need to be machined, and their positions are at 9 o'clock and 3 o'clock. The dimensions are designed according to the following formula. R=0.4d, g=0.025d, where R is the depth of the depression and d is the shaft diameter.
3. Greasing lubrication: Greasing lubricated bearings are generally used for equipment that rotates slowly or swings without the need for slotting.