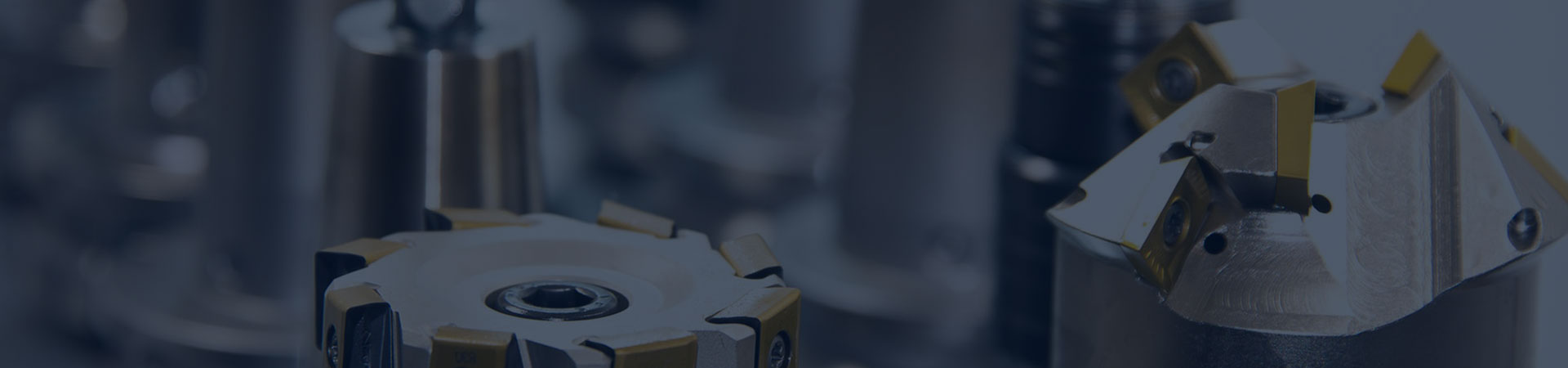
Methods of Extending Steel Wire Rope Useful Life
Ropes with compacted strands
One of the effective ways to extend steel wire rope lifespan is to make it with compacted strands. Before the strands are braid into a steel wire rope they are exposed to radiate swaging which cause wire deformation resulting into solidified structure and dense cross section. In the process of swaging, the outer diameter of the strand decreases, the metal cross-section area increases, since the voids between the wires inside the strand are filled. The surface of the strand becomes smoother.
Overview
Improving of strand contact conditions
Reducing of contact pressures
Advantages of compacted strands:
• Rope with swaged strands have higher tensile strength comparing to regular ropes of all diameters.
• Wires in swaged strands have smother contact with each other comparing to round wires of regular strands.
• Smooth surface of swaged strands provides better contact with surface of pulleys and drums resulting in higher
endurance of equipment and of the rope itself.
• Ropes with swaged strands have high abrasive wear and flexural fatigue resistance.
• Contact between outer strands and contact between layers of rope on the drum are far better comparing to regular
round strand ropes.
A core with polymer coating:
Steel wire rope with polymer coated metal core consists of layer of strand braided around metal core which is covered in polymer using extrusion method. Polymer coating drastically reduces possible glide between rope elements and prevents geometrical change of the rope.
Plastic covering has the following purposes:
• Creation of physical bound that fixates positions of certain components of steel wire rope and provides their required shift.
• Reducing of internal corrosion caused by pollutants due to higher hermetic state of the rope.
• Filling of gaps between outer strands and core to eliminate wear.
• Special type polymer is created to be used between -35 and +90 without dimensional change or breaks.
• Stabilizing effect of plastic coating is seen the most during influence of lateral thrust, rotation, caused by wide deviation angle on pulleys, influence of impact stress.
Extending Steel Wire Rope Useful Life through Precision Lubrication:
Steel wire rope needs lubrication during the manufacturing process. The lubricant helps the wires move smoothly through manufacturing machines. Also, it helps create a protective layer between the wires to allow slight movement between them and minimize the risk of wear and corrosion.
Steel wire rope needs lubrication during storage. Direct exposure to rain or snow, humidity, temperature changes, and chemicals increases the risk of corrosion before deployment. Regular wire rope inspections during storage can help determine when relubrication is necessary. Signs of wear, corrosion, or excess dirt and debris may show the need for relubrication.
Steel wire rope needs lubrication in service. Lubrication helps to minimize the effects of these factors by:
Reducing internal (metal-to-metal contact between wires and strands) and external friction (wire rope exterior surfaces with grooves).
Enhancing flexibility.
Mitigating fatigue failure.
Protecting from external contaminants.
Preventing Corrosion.
A steel wire rope that is properly lubricated (Right Lubricant, Right Quantity, Right Method) will last three times as many working hours or cycles as one that is poorly lubricated. An improvement of up to 300% can be expected from a correctly lubricated rope compared with a similar unlubricated rope.