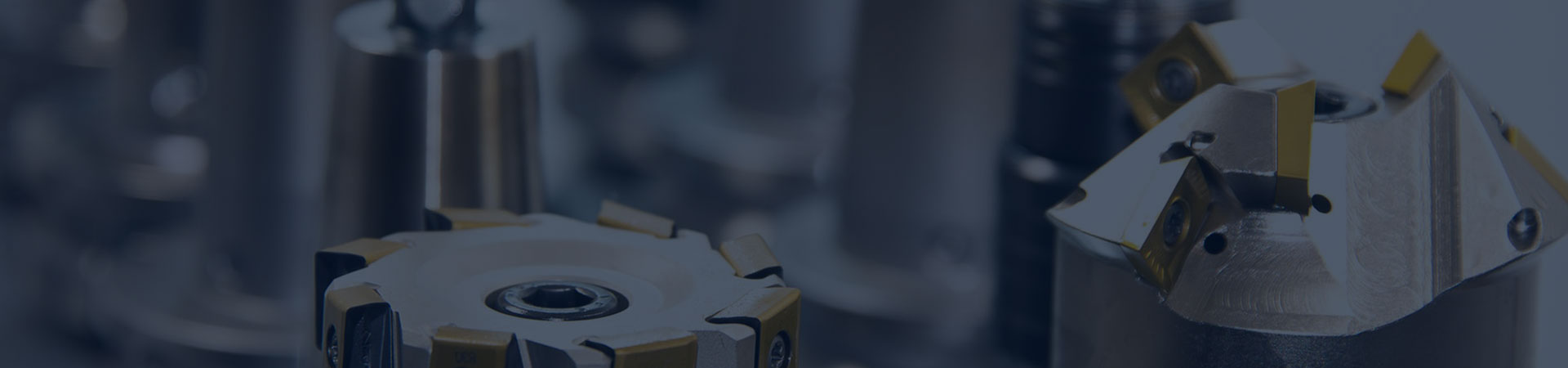
Installation of Wire Rope
Overview
Uncoiling of Wire Rope:
When uncoiling wire rope, the reel should be placed on a dedicated rack, and the reel should be rotated slowly (see Figure 1). If the wire rope becomes tangled during uncoiling, stop immediately, eliminate the tangle, and then continue.
Figure 1
Arrangement of Wire Rope on the Reel:
The winding direction of the wire rope on the reel must be arranged according to the lay direction of the wire rope, with right hand lay ropes arranged from left to right and left hand lay ropes arranged from right to left (see Figure 2).
Figure 2
The wire rope should be neatly wound on the reel to avoid deviation or jamming.
The wire rope should be wound under tension (see Figure 3), especially for multi-layer winding. If the first layer is not wound tightly, the wire rope is prone to collapse when winding the second layer. This can cause damage to the wire rope when it is under load.
After the new wire rope is installed, it should be operated under approximately 10% of its rated load for several cycles to ensure that the wire rope is firmly wound on the drum. This is especially important when a tower crane has had its rope changed at height; the rope should be run several times with light load.
Figure 3
Wire Rope Cutting:
When cutting a wire rope, tie the two sides of the cutting area with iron wire, with a distance of 10-20mm between them, and the tying length should be 2-4 times the rope diameter. Then, cut with a cutting tool (see Figure 4).
Improper cutting can cause individual strands to loosen, leading to individual external femoral arch when it is in operation. Additionally, for multi-layer wire ropes, it is advisable to use gas welding for cutting, or cut with a cutting tool first and then weld the ends securely with electric welding.
Figure 4
Key Node Control:
1. When replacing the wire rope, check the condition of the pulley and the drum rope groove to ensure there are no defects such as ripples.
2. The effective diameter of the pulley rope groove should be 5% to 10% larger than the nominal diameter of the wire rope, and at least 1% larger than the actual diameter of the new wire rope.
3. For multi-layer wound wire ropes, apply a tension force during installation that is approximately 1% to 2% of the minimum breaking force of the wire rope. This helps ensure that the bottom layer of wire rope is wound firmly, providing a stable foundation for subsequent wire ropes.
4. During installation, avoid any friction between the wire rope and any part of the hoisting machine or hoist.
5. Use professional equipment to assist in the cable winding process. The use of electric winding machines is efficient, with fully automatic rope control for high efficiency and a wide range of tension adjustment.