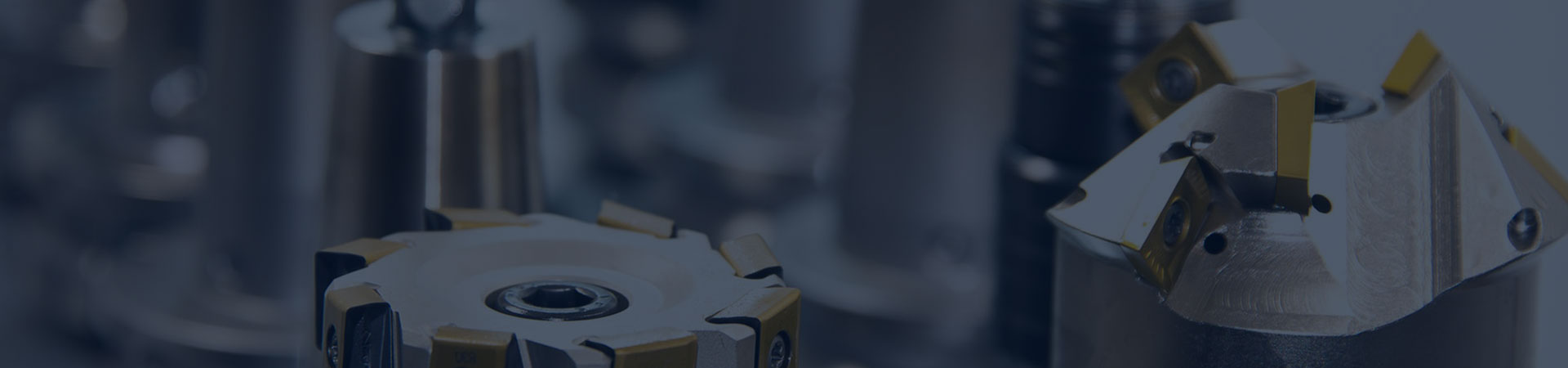
Fault Analysis and Troubleshooting of Marine Air Compressors
Marine air compressors may experience various malfunctions during long-term operation.
Common faults: inability to start, high exhaust temperature, decreased exhaust volume, insufficient output pressure, abnormal knocking sound, etc.
Overview
Common faults and their causes
1. Unable to start
Cause analysis:
Power failure: such as power failure, blown fuse, damaged switch, etc.
Control circuit failure: such as control components such as relays and contactors malfunctioning.
Startup failure: such as damaged starting capacitor, malfunctioning starting button, etc.
Troubleshooting:
Check the power circuit to ensure that the power is connected.
Check and replace blown fuses, repair or replace damaged switches.
Check and replace faulty relays and contactors.
Check the starting capacitor and replace it if necessary; Check the start button and its wiring.
2. Overheating
Cause analysis:
Cooling system malfunction: such as insufficient cooling water, cooler blockage, etc.
Poor lubrication: Insufficient lubricating oil or poor oil quality.
Compressor overload: Continuous operation time is too long or the load is too high.
Troubleshooting:
Check the cooling water system to ensure sufficient water volume and clean the cooler.
Check the amount and quality of lubricating oil, and supplement or replace lubricating oil if necessary.
Reasonably arrange the running time of the compressor to avoid prolonged overload operation.
3. The exhaust temperature is too high
Cause analysis:
Excessive exhaust pressure;
Leakage of air valve;
Poor cooling;
The suction temperature is too high.
Troubleshooting:
Check the cause and eliminate it;
Repair or replace the air valve;
Improve cooling conditions;
Check the cause and eliminate it.
4. Decreased exhaust volume
Cause analysis:
Speed decrease;
leak;
Excessive clearance volume;
Poor cooling;
Dirty and clogged suction filter
Troubleshooting:
Adjust the speed;
Check the cause and arrange it accordingly;
Adjust the clearance;
Strengthen cooling;
Clean the filter.
5. Insufficient output pressure
Cause analysis:
Inhalation filter blockage: Air filter blockage leads to insufficient intake.
Valve malfunction: The intake and exhaust valves are worn, cracked, or stuck.
Wear of piston rings: Severe wear of piston rings leads to a decrease in compression efficiency.
Leakage: Leakage in pipelines, joints, or seals.
Troubleshooting:
Check and clean or replace the suction filter.
Check the intake and exhaust valves, repair or replace damaged valves.
Check the piston rings and replace them if necessary.
Check the pipelines and joints, repair or replace the sealing components of the leaking parts.
6. Abnormal tapping sound
Cause analysis:
Excessive bearing clearance;
Loose fasteners;
The residual limit of the cylinder is too small;
Liquid hammer;
Poor alignment between the crankshaft and cylinder;
Foreign objects entering the cylinder
Troubleshooting:
Adjust the gap;
Tighten again;
Adjust the clearance;
Check the cause of liquid hammer and eliminate it;
Recalibrate;
Check and remove foreign objects
7. Interstage pressure too low
Cause analysis:
Leakage of inter stage cooler;
The exhaust volume of the front stage has decreased.
Troubleshooting:
Check for leaks and repair them;
Check the cause and eliminate it.
8. Interstage pressure too high
Cause analysis:
Poor inter stage cooling;
Reduced exhaust volume in the rear stage;
Poor sealing of piston rings.
Troubleshooting:
Strengthen cooling;
Check the cause and eliminate it;
Replace the piston rings.
Fault prevention measures
1. Regular maintenance
Regularly inspect and maintain all components, clean or replace vulnerable parts such as filters and lubricating oil in a timely manner.
Regularly check the tightness of each connecting part to prevent loosening.
2. Correct operation
Strictly follow the operating procedures to avoid equipment damage caused by illegal operations.
Reasonably arrange the running time of the compressor to avoid prolonged overload operation.
3. Monitoring equipment status
By monitoring the operating parameters of the equipment, such as pressure, temperature, noise, etc., abnormal situations can be detected and handled in a timely manner.
Use fault diagnosis equipment to regularly perform fault detection on the compressor and prevent the occurrence of major faults.
By analyzing and eliminating common faults of marine air compressors, and taking corresponding preventive measures, the reliability and service life of equipment can be effectively improved, ensuring the safe operation of ships.
For more marine air compressor information, please click here.