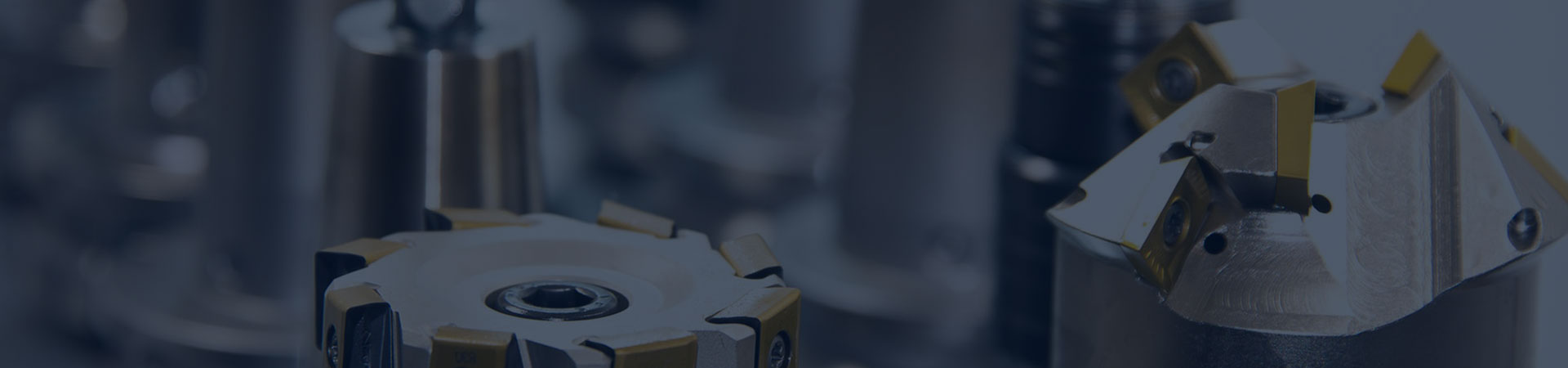
Casting process of container securing fittings
Wax injection
Assembly of the wax stick
Ceramic shell building
De-wax
Conventional casting
Knock-out
Cut-off the parts
Finished metal investment castings
Overview
Wax injection
Wax models of the desired precision castings are produced by injection moulding or by using rapid prototyping. These prototypes are directly produced from CAD data files. The wax models of the prototypes are referred to as patterns.
Assembly of the wax stick
Patterns are then attached to a central wax stick, called the gating system, to produce a former on which to build up a ceramic shell.
Ceramic shell building
The shell is built by alternately immersing the wax model in liquid ceramic slurry and placing it in a bed of fine sand. Up to eight layers can be applied in this manner, depending on the shape and weight of the part.
De-wax
Once the ceramic shell is dry, the wax former is melted out, creating a negative impression of the assembly within the ceramic and sand shell.
Conventional casting
Molten metal is gravity poured into the ceramic shell. As the metal solidifies and cools, the part, the gating system, the sprue and the pouring cup become one solid casting.
Knock-out
Once the metal is solid and cool the ceramic shell is broken off.
Cut-off of parts
The gating system and sprues are then cut away using a high speed saw.
Finished metal investment castings
Following further operations such as machining, galvanizing, assembly, final quality control and classification society approval, the precision metal castings, identical to the original wax patterns, are ready for shipment to the customer.